Chemical Polishing Basics
Chemical polishing is one of metal surface finishing technologies used for stainless steel and other kinds of metals commonly used as mechanical components, such as copper, steel, aluminum, and titanium alloy. The technology can be applied to a broad range of shapes and sizes, but it is especially useful for tubing. The inside wall of any length and diameter of tubes, and capillaries, stright or curved, simple or complex in shape, can be polished with an impressive surface roughness characteristics.
It dissolves and removes microscopic scale burrs, causing uneven surfaces, by submerging the component into an acidic chemical bath. Fundamentally, it is a chemical etching process that can remove micron size features on a metal surface. Compared with the surface prior to polishing, unevenness of the surface is reduced and thus the surface becomes flatter and smoother.
Chemical polishing allows microburr removal, smoother and polished surface finish, corrosion resistance enhancement, surface absorption and outgassing reduction, and reflectiviey improvement. As long as the polishing chemical can make a contact to the metal surface, no matter how complex the shape of the metal parts, polishing can happen.
Chemical polishing can be applied in a variety of fields such as preision machinery, semiconductor, medical equipment, nuclear power industry, aviation, food industy, and hardware tools.
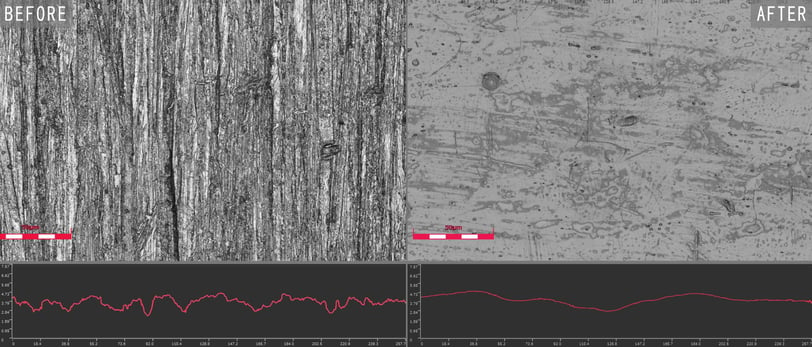
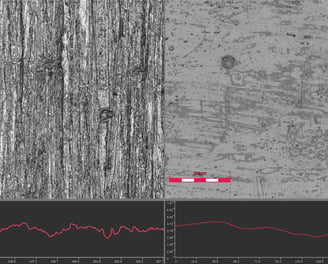
Electropolishing vs. Chemical Polishing
In the electropolishing process, a low voltage DC power source and acidic liquid bath is used. A metal plate is connected to the cathode (-) while the parts to be polished are connected to the anode (+). When the voltage is applied, an electrochemical response occurs and starts to etch the anode metal surfaces. In principle, corrosion happens where the electric charge is higher in location, thereby improving the smotthness on the surface. The process eliminates burr and hardened layer created after machining. Electropolished pipes improve the flow rate inside the pipe, as the micro cavities of the roughness in the pipes can significantly slow down the flow rate. In addition, bacterial colony growth can be eliminated. The process also improves corrosion resistance.
Chemical polishing, on the other hand, uses a special chemical solution, where a stainless steel component is immersed. There is no need of using electricity, the process selectively dissolves extruded surfaces. After a series of washing and cleaning processes, the parts turn bright and shiny, indicating a significant amount of surface polishing. This process is straightforward, ultimately achieving the results similar to the pipes polished using electropolishing. Therefore, parts with practically any size and shape can be polished.
Chemical polishing can be advantageous for small diameter tubes, as the electrode must be placed inside the pipe if electropolishing can be used. Due to the distribution of electricity in the pipe after the cleaning process, only relatively large diameter pipes can be treated if electropolishing is used. Pipes with a small diameter and curved pipes cannot be treated evenly, with the sub-optimal results. In addition, electropolishing is more complex than chemical polishing.
with chemical polishing, pipes with the dameters rangiing between 3 mm and 400 mm, with the lendth of 6 meters or even longer can be polished. Polishing depth can range between 0.01 ~ 0.05 mm, with the surface roughness down to approximately 0.05 um and better.
lmproving Effective Surface Area by Chemical Polishing
After an ordinary stainless steel plate or tube goes through a series of machining processes, the inner and outer wall surfaces will alter their characteristics, with the indicators such as roughness, burr, hardened layer, etc. As a result, the effective surface area of typical stainless steel pipes without electropolishing or chemical polishing is much larger than the geometrical surface area, which is a simple calculation of the area assuming the surface is perfectly flat.
The surface roughness and burr cause sticking and abserption of small particles, slowing the flow rate of the medium, clogging the tube, bacterial colony growth and many other undesired characteristics. An electropolishing or chemical polishing process must be used to meet the demanding requirements of highly demanding equipment manufacturing technology. For example, after the tubes used in a milk processing plant are replaced, he shelf time of milk increase significantly, thanks to the reduction of unwanted substance added to milk, causing premature degradation.
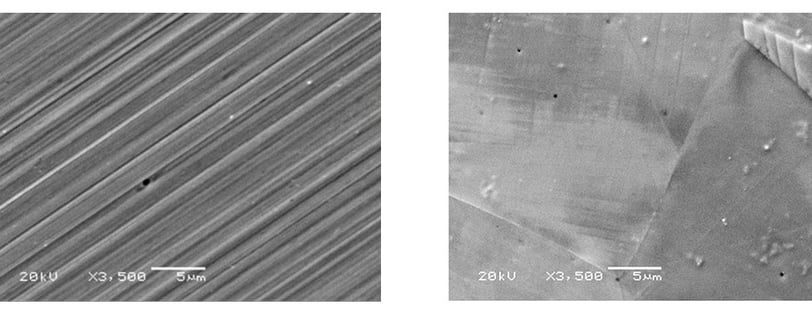
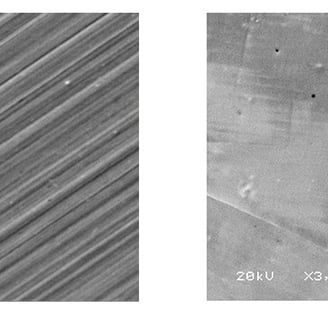